
Yea, I saw that video years ago, crazy that it's still around.
I don't know if anyone has worked on any 1.8t's or not but here's one we've got at the shop. It's all mocked up and damn is it a tight fit up top.
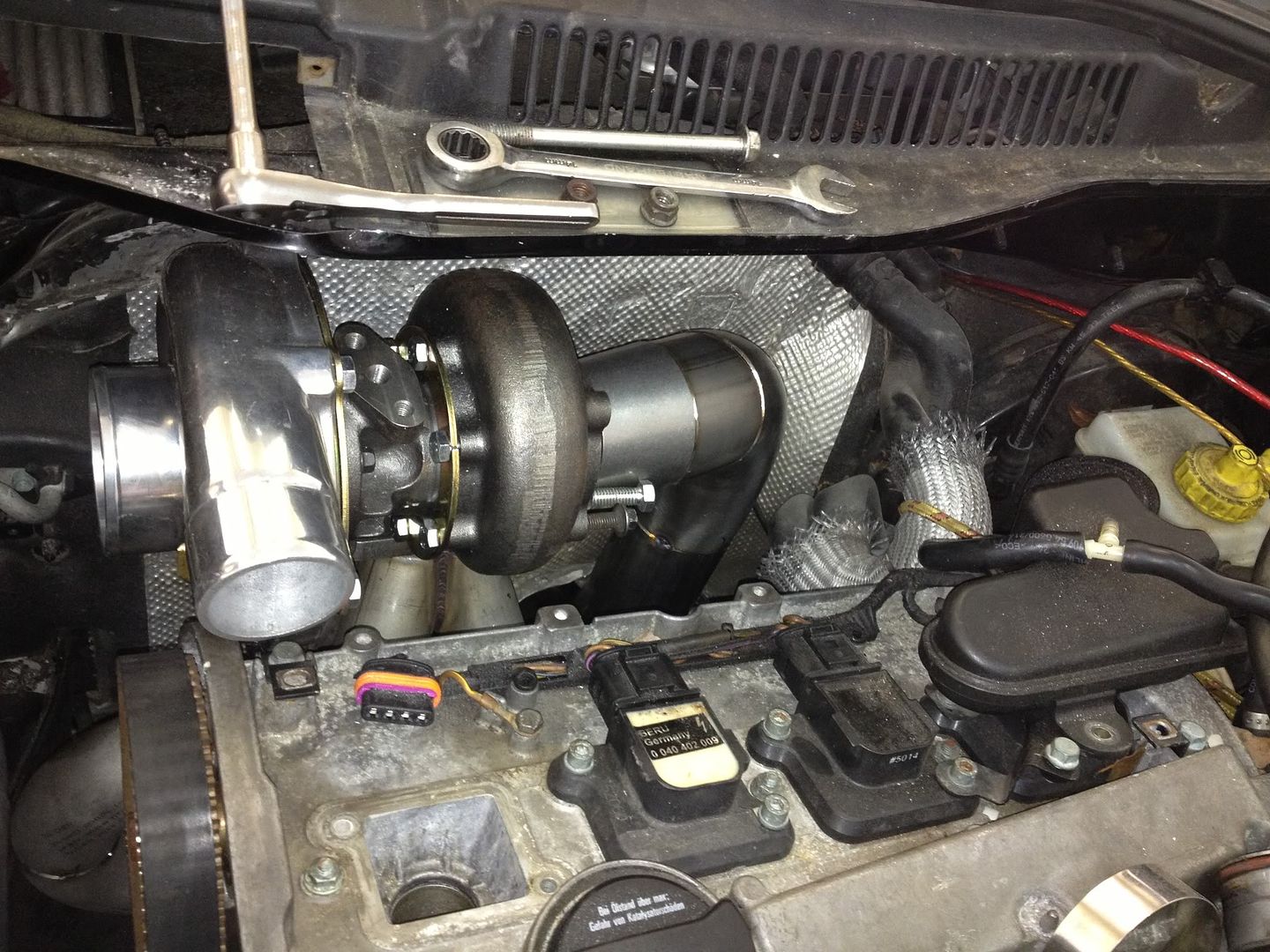
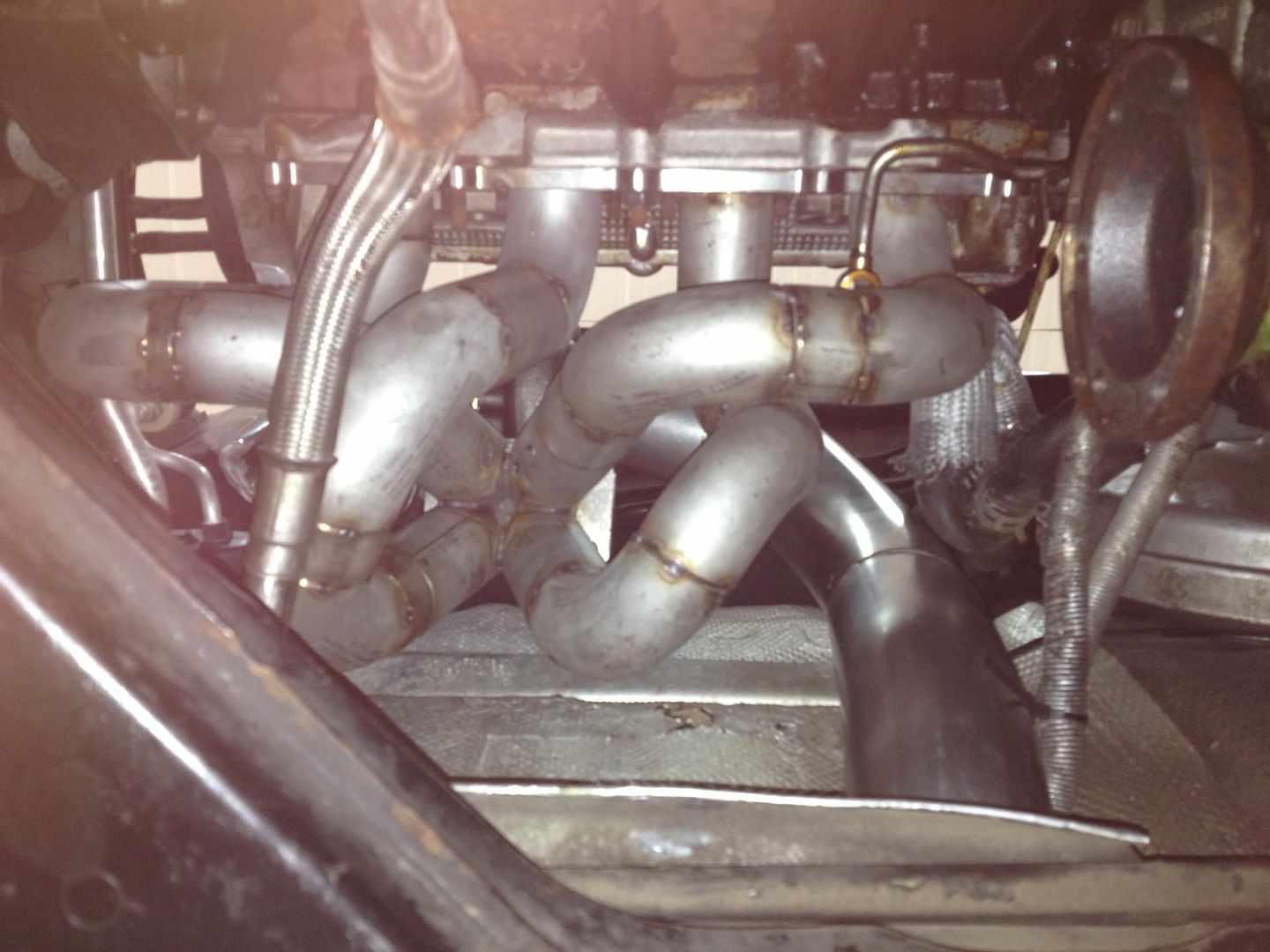
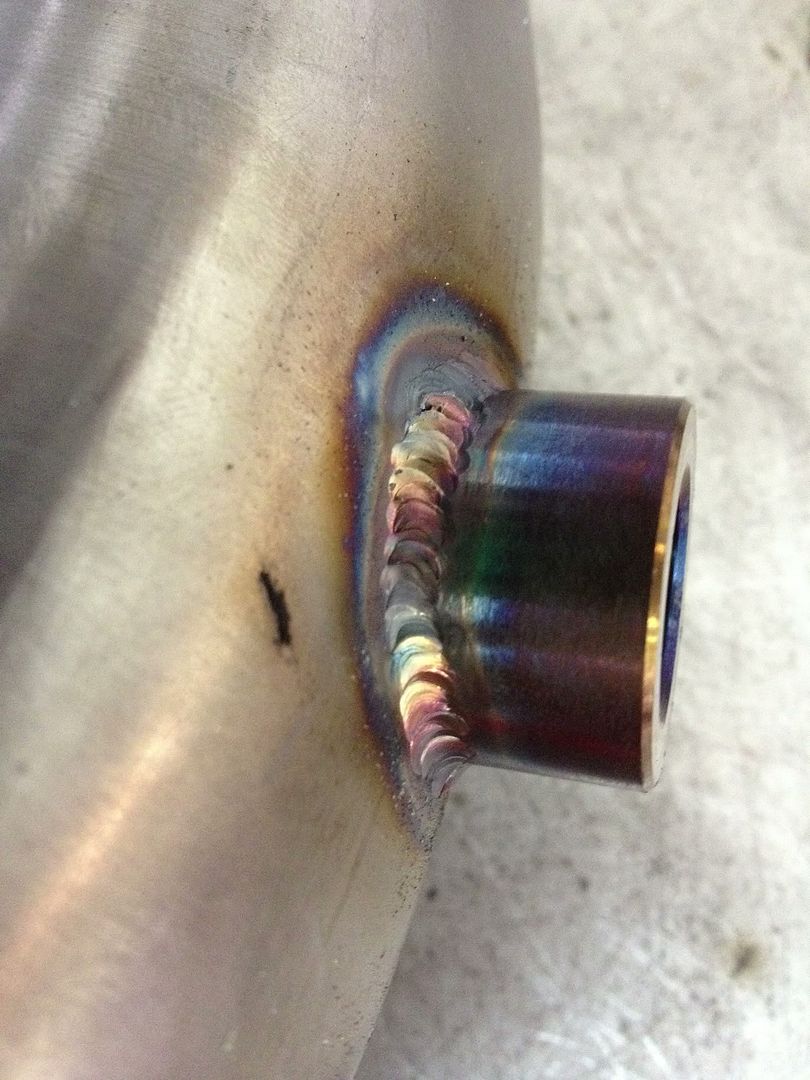
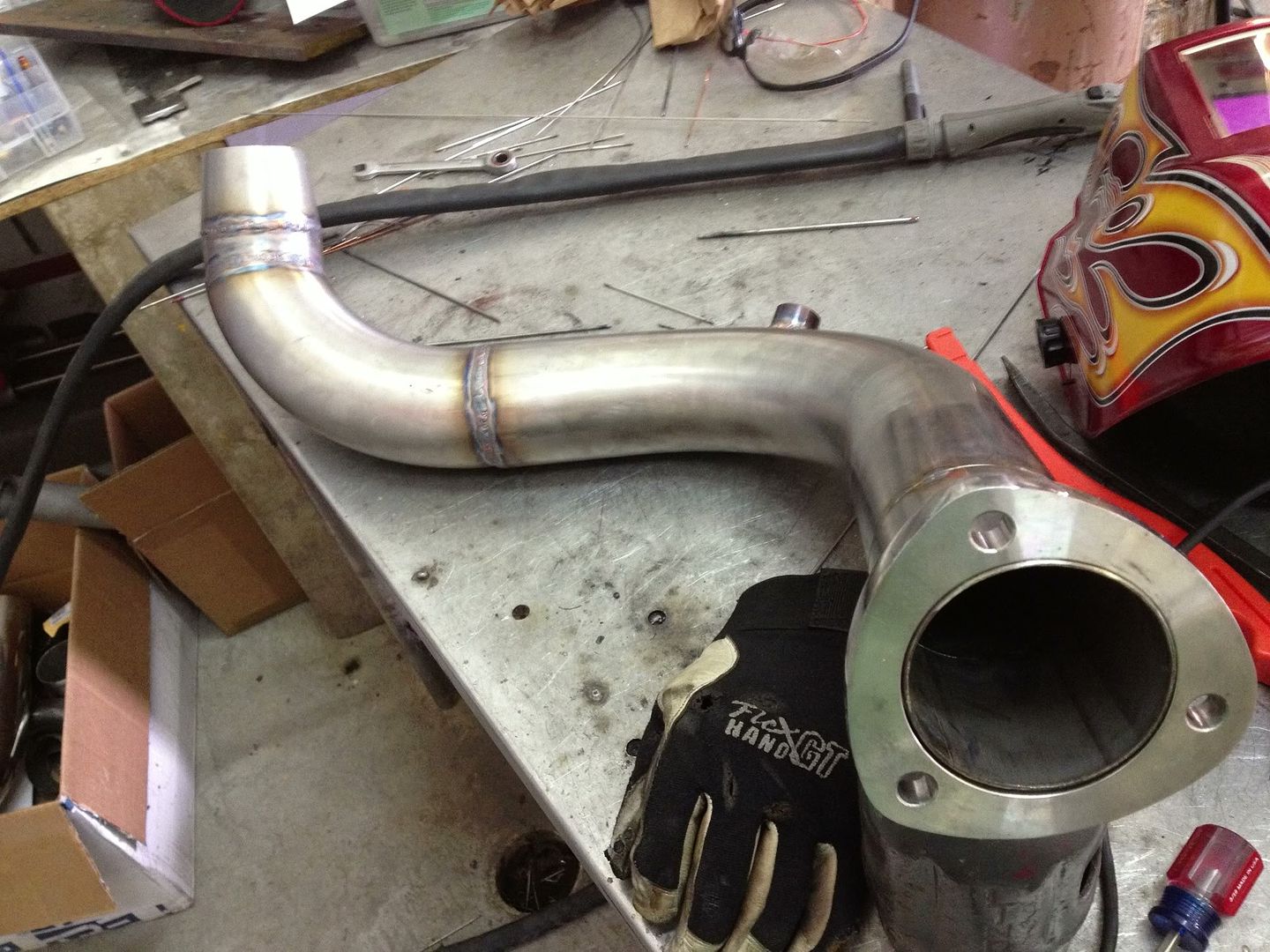
Downpipe still needs a flex welded in but it's almost done. Should have it all buttoned up beginning of next week.
I don't know if anyone has worked on any 1.8t's or not but here's one we've got at the shop. It's all mocked up and damn is it a tight fit up top.
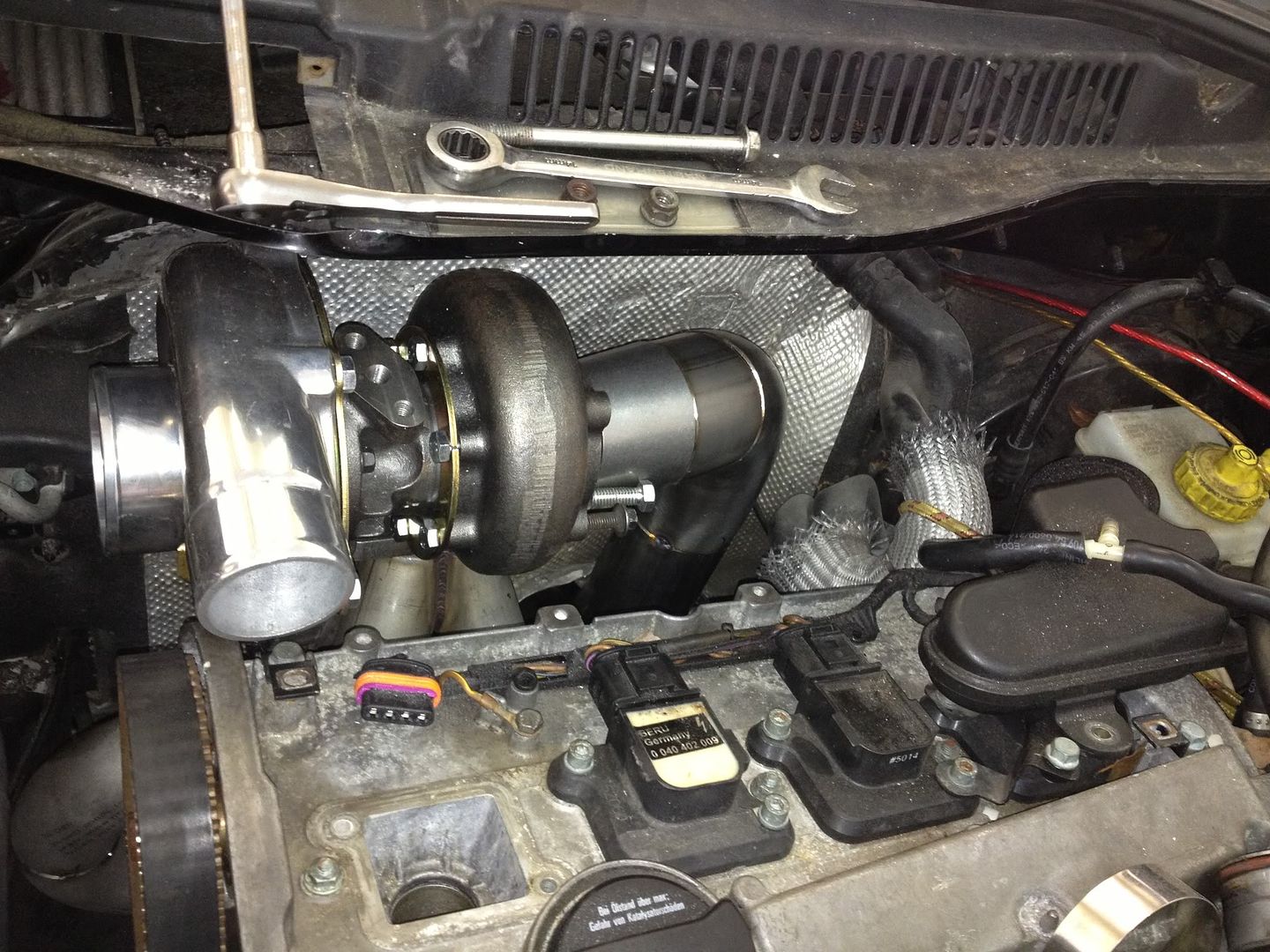
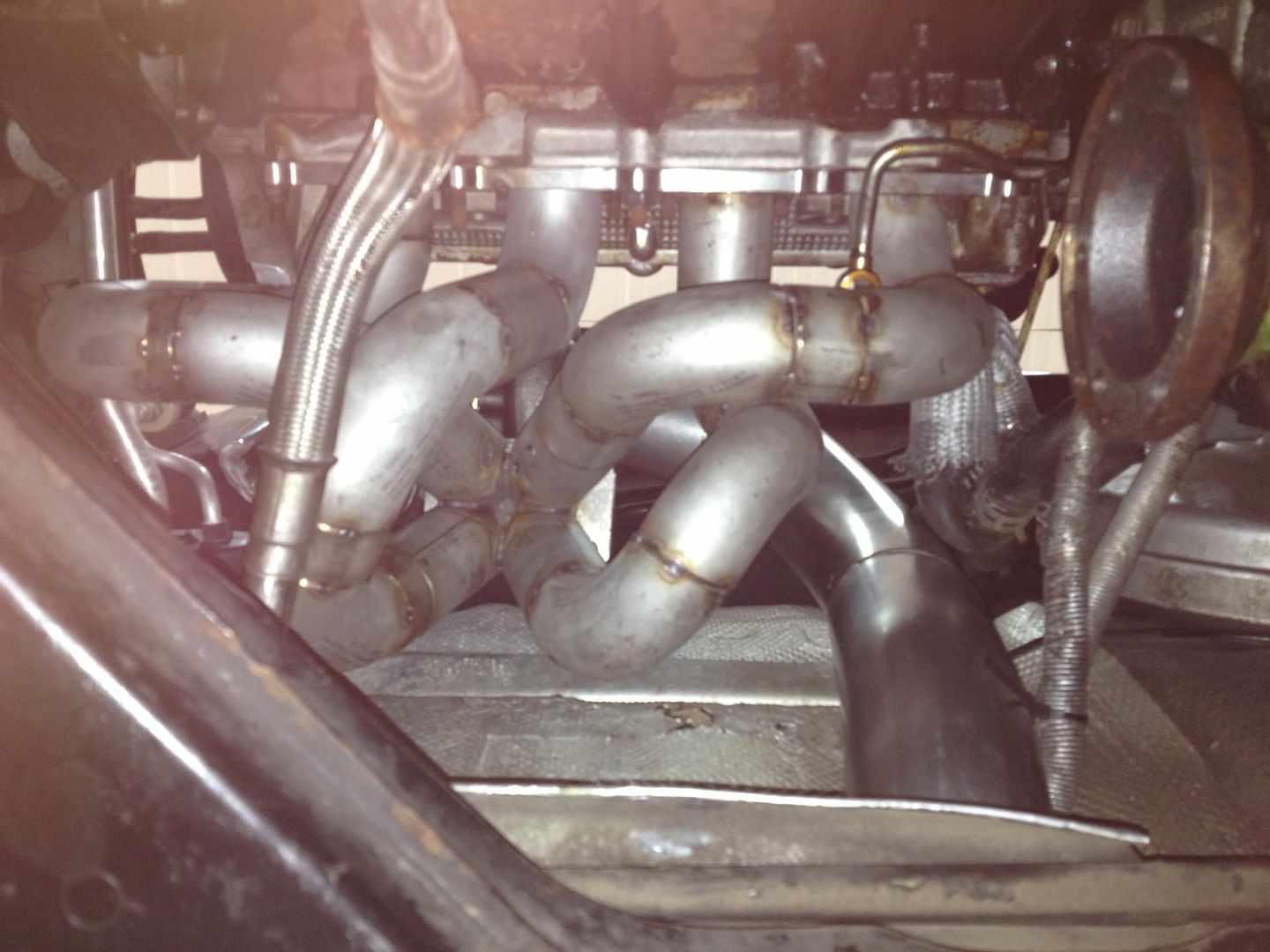
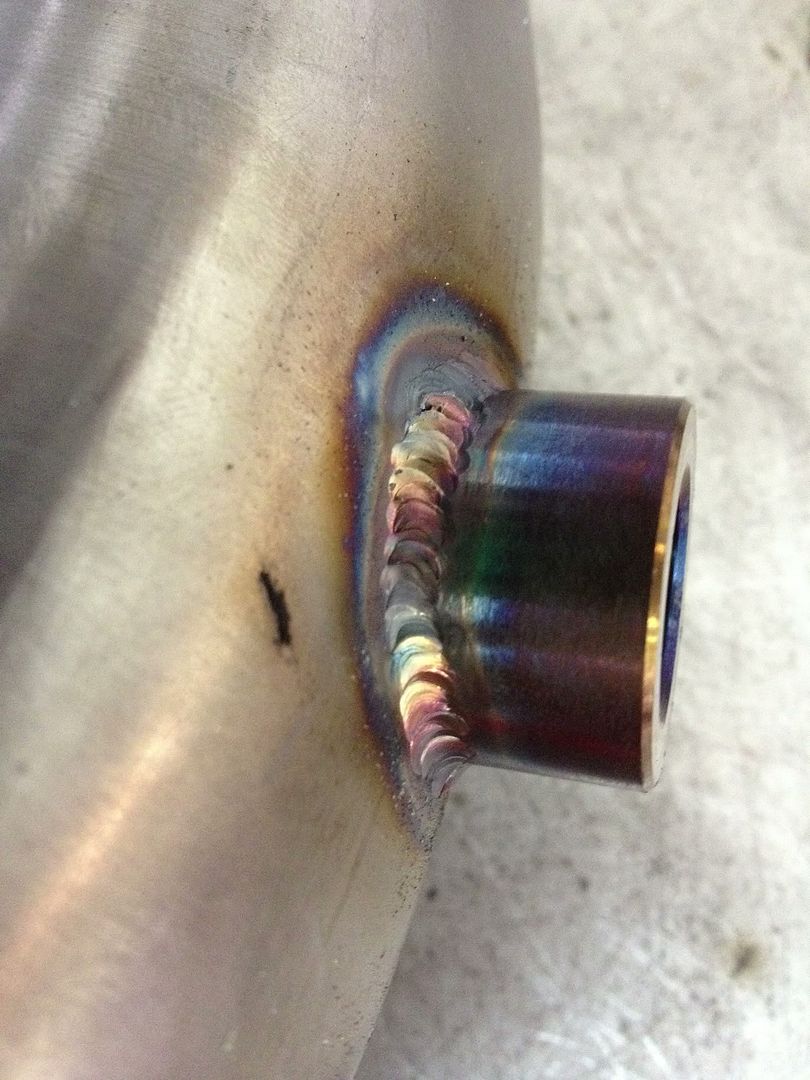
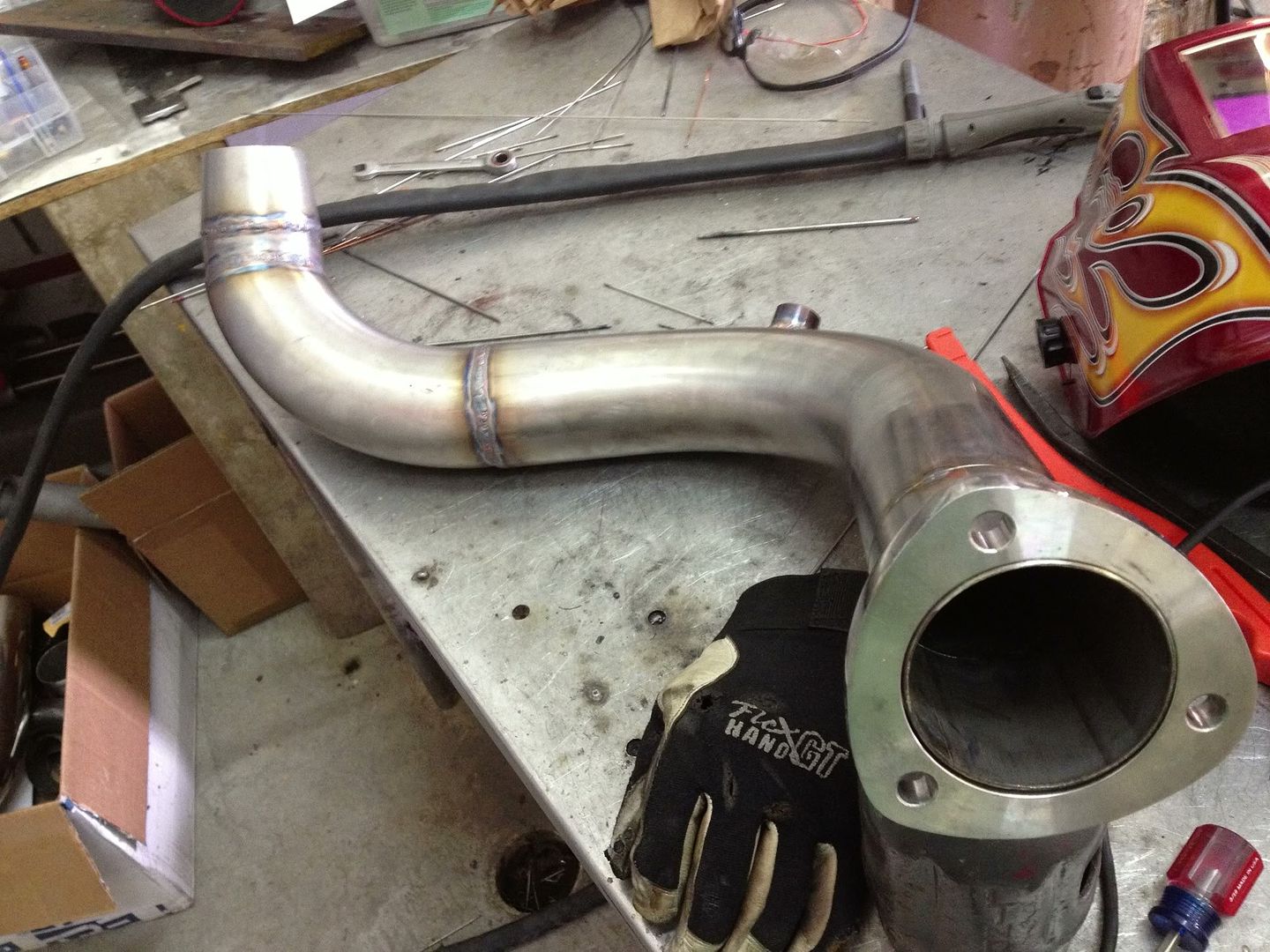
Downpipe still needs a flex welded in but it's almost done. Should have it all buttoned up beginning of next week.