
I've been looking at rims lately and have been comparing new and pre-owned forged rims as well as lightweight brand new wheels. I looked for a thread on that subject and came up empty. Figured I'd start one. Feel free to add to my list with pics and specs, or links and I'll go grab the photo and information.
I'm looking at 15" only in this thread, less than 14 pounds, and in an offset that will easily bolt onto our cars. I am following a quip by Mike K and generally looking at 6 1/2" - 7" wide, in a 30-35 mm offset.
For reference our Nissan OEM B14 SE-R rim is 15"X6", 4X100 bolt pattern, has a 40mm offset, 59mm center bore, and weighs in at 17 or so pounds.
Tire Wheel Sizes
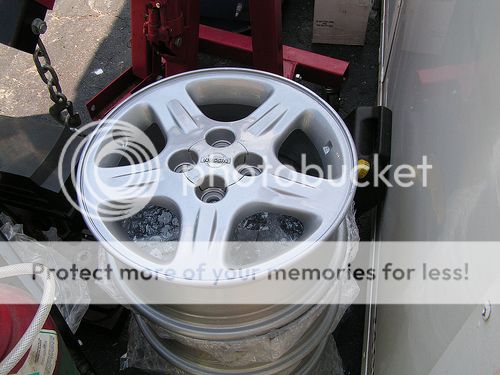
Here are some additional pertinent links:
Good-Win-Racing They are very knowledgeable and carry a variety of very lightweight and affordable wheels in our size and offset parameters.
Miata Wheels and Tires - Mazda Performance Parts
Measure Speed for aftermarket wheel weights:
http://http://measurespeed.com/index.php
Wheel Weight Chart (originally from wheelweights dot net) Overwhelming amounts of info on both OEM and aftermarket wheels.
http://http://www.evolutionm.net/forums/evo-tires-wheels-brakes-suspension-sponsored-tire-rack/52485-wheel-weight-chart-most-listed-must-see.html
Miata Dot Net Faq on wheel weights Tons of info including what factory OEM wheels from other manufacturers will fit on a Miata. If it fits a Miata, chances are very high it fits our rides.
http://www.miata.net/faq/wheel_weights.html
Tire Rack explains the different types of wheel construction:
http://www.tirerack.com/wheels/tech/techpage.jsp?techid=90
Originally Posted by Tire
What Is a Wheel and What Is a Rim? Are They the Same Thing?
It may seem obvious, but a wheel is comprised of a hub, spokes and rim. Sometimes these components will be one piece, sometimes two or three. The hub is the center portion of the wheel and is what attaches the wheel to the suspension. The spokes radiate out from the hub and attach to the rim. The rim is the outer part of the wheel that holds the tire. While many people refer to wheels as "rims," this is technically incorrect. We'll discuss several ways that wheels are manufactured below.
One-Piece Cast Wheels
This is the most common type of aluminum wheel. The casting of wheels is the process of getting molten aluminum inside a mold to form a wheel. There are different ways this can be accomplished and although it sounds simple, this is truly an art when done properly.
Gravity Casting
Gravity casting is the most basic process of pouring molten aluminum into a mold utilizing the earth's gravity to fill the mold. Gravity casting offers a very reasonable production cost and is a good method for casting designs that are more visually oriented or when reducing weight is not a primary concern. Since the process relies on gravity to fill the mold, the aluminum is not as densely packed in the mold as some other casting processes. Often gravity cast wheels will have a higher weight to achieve the required strength.
Low Pressure Casting
Low pressure casting uses positive pressure to move the molten aluminum into the mold quicker and achieve a finished product that has improved mechanical properties (more density) over a gravity cast wheel. There is a slightly higher production cost over gravity casting, but low pressure casting is the most common process approved for aluminum wheels sold to the O.E.M. market. Some companies offer wheels that are produced under a higher pressure in special casting equipment to create a wheel that is lighter and stronger than a wheel produced in low pressure, but there's a higher cost associated with the process. Low pressure cast wheels offer a good value for the aftermarket while still maintaining strength and a lighter weight.
Spun-Rim, Flow-Forming or Rim Rolling Technology
This specialized process begins with a low pressure type of casting and uses a special machine that spins the initial casting, heats the outer portion of the casting and then uses steel rollers pressed against the rim area to pull the rim to its final width and shape. The combination of the heat, pressure and spinning create a rim area with the strength similar to a forged wheel without the high cost of the forging. Some of the special wheels produced for the O.E.M. high performance or limited production vehicles utilize this type of technology resulting in a light and strong wheel at a reasonable cost. O.Z. has used this technology for several years in their production of racing wheels for Formula One and Indy cars. O.Z.'s Formula HLT wheel for the aftermarket is an example of a wheel produced using spun rim technology.
Forged
The ultimate in one-piece wheels. Forging is the process of forcing a solid billet of aluminum between the forging dies under an extreme amount of pressure. This creates a finished product that is very dense, very strong and therefore can be very light. The costs of tooling, development, equipment, etc., make this type of wheel very exclusive and usually demand a high price in the aftermarket.
Multi-Piece Wheels
This type of wheel utilizes two or three components assembled together to produce a finished wheel. Multi-piece wheels can use many different methods of manufacturing. Centers can be cast in various methods or forged. The rim sections for 3-piece wheels are normally spun from disks of aluminum. Generally, spun rim sections offer the ability to custom-tailor wheels for special applications that would not be available otherwise. The rim sections are bolted to the center and normally a sealant is applied in or on the assembly area to seal the wheel. This type of 3-piece construction was originally developed for racing in the early 1970s and has been used on cars ever since. The 3-piece wheels are most popular in the 17" and larger diameters.
There are now many options for 2-piece wheels in the market. The 2-piece wheel design does not offer as wide a range of application that a 3-piece wheel allows, however they are more common in the market and the prices start well below the average 3-piece wheel. Some 2-piece wheels have the center bolted into a cast or cast/spun rim section and other manufacturers press centers into spun rim sections and weld the unit together. When BBS developed a new 2-piece wheel to replace the previous 3-piece street wheel, they used the special rim-rolling technology (originally developed for racing wheels) to give the rim section the weight and strength advantages similar to a forged rim. On the high-end of the 2-piece wheel market you can find wheels using forged rims and forged centers. Since these are only sold in small volume and due to the high development and production costs associated with the forging process, they tend to be on the high end of the price scale.
Pro Tip: At Tire Rack, type in that you own a 1990 Mazda Miata. Then look at the 15" lightweight wheel selection.
I'm looking at 15" only in this thread, less than 14 pounds, and in an offset that will easily bolt onto our cars. I am following a quip by Mike K and generally looking at 6 1/2" - 7" wide, in a 30-35 mm offset.
For reference our Nissan OEM B14 SE-R rim is 15"X6", 4X100 bolt pattern, has a 40mm offset, 59mm center bore, and weighs in at 17 or so pounds.
Tire Wheel Sizes
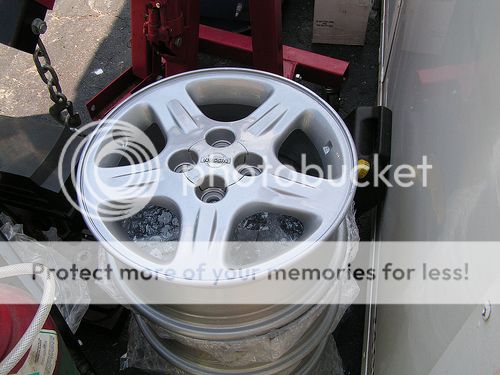
Here are some additional pertinent links:
Good-Win-Racing They are very knowledgeable and carry a variety of very lightweight and affordable wheels in our size and offset parameters.
Miata Wheels and Tires - Mazda Performance Parts
Measure Speed for aftermarket wheel weights:
http://http://measurespeed.com/index.php
Wheel Weight Chart (originally from wheelweights dot net) Overwhelming amounts of info on both OEM and aftermarket wheels.
http://http://www.evolutionm.net/forums/evo-tires-wheels-brakes-suspension-sponsored-tire-rack/52485-wheel-weight-chart-most-listed-must-see.html
Miata Dot Net Faq on wheel weights Tons of info including what factory OEM wheels from other manufacturers will fit on a Miata. If it fits a Miata, chances are very high it fits our rides.
http://www.miata.net/faq/wheel_weights.html
Tire Rack explains the different types of wheel construction:
http://www.tirerack.com/wheels/tech/techpage.jsp?techid=90

What Is a Wheel and What Is a Rim? Are They the Same Thing?
It may seem obvious, but a wheel is comprised of a hub, spokes and rim. Sometimes these components will be one piece, sometimes two or three. The hub is the center portion of the wheel and is what attaches the wheel to the suspension. The spokes radiate out from the hub and attach to the rim. The rim is the outer part of the wheel that holds the tire. While many people refer to wheels as "rims," this is technically incorrect. We'll discuss several ways that wheels are manufactured below.
One-Piece Cast Wheels
This is the most common type of aluminum wheel. The casting of wheels is the process of getting molten aluminum inside a mold to form a wheel. There are different ways this can be accomplished and although it sounds simple, this is truly an art when done properly.
Gravity Casting
Gravity casting is the most basic process of pouring molten aluminum into a mold utilizing the earth's gravity to fill the mold. Gravity casting offers a very reasonable production cost and is a good method for casting designs that are more visually oriented or when reducing weight is not a primary concern. Since the process relies on gravity to fill the mold, the aluminum is not as densely packed in the mold as some other casting processes. Often gravity cast wheels will have a higher weight to achieve the required strength.
Low Pressure Casting
Low pressure casting uses positive pressure to move the molten aluminum into the mold quicker and achieve a finished product that has improved mechanical properties (more density) over a gravity cast wheel. There is a slightly higher production cost over gravity casting, but low pressure casting is the most common process approved for aluminum wheels sold to the O.E.M. market. Some companies offer wheels that are produced under a higher pressure in special casting equipment to create a wheel that is lighter and stronger than a wheel produced in low pressure, but there's a higher cost associated with the process. Low pressure cast wheels offer a good value for the aftermarket while still maintaining strength and a lighter weight.
Spun-Rim, Flow-Forming or Rim Rolling Technology
This specialized process begins with a low pressure type of casting and uses a special machine that spins the initial casting, heats the outer portion of the casting and then uses steel rollers pressed against the rim area to pull the rim to its final width and shape. The combination of the heat, pressure and spinning create a rim area with the strength similar to a forged wheel without the high cost of the forging. Some of the special wheels produced for the O.E.M. high performance or limited production vehicles utilize this type of technology resulting in a light and strong wheel at a reasonable cost. O.Z. has used this technology for several years in their production of racing wheels for Formula One and Indy cars. O.Z.'s Formula HLT wheel for the aftermarket is an example of a wheel produced using spun rim technology.
Forged
The ultimate in one-piece wheels. Forging is the process of forcing a solid billet of aluminum between the forging dies under an extreme amount of pressure. This creates a finished product that is very dense, very strong and therefore can be very light. The costs of tooling, development, equipment, etc., make this type of wheel very exclusive and usually demand a high price in the aftermarket.
Multi-Piece Wheels
This type of wheel utilizes two or three components assembled together to produce a finished wheel. Multi-piece wheels can use many different methods of manufacturing. Centers can be cast in various methods or forged. The rim sections for 3-piece wheels are normally spun from disks of aluminum. Generally, spun rim sections offer the ability to custom-tailor wheels for special applications that would not be available otherwise. The rim sections are bolted to the center and normally a sealant is applied in or on the assembly area to seal the wheel. This type of 3-piece construction was originally developed for racing in the early 1970s and has been used on cars ever since. The 3-piece wheels are most popular in the 17" and larger diameters.
There are now many options for 2-piece wheels in the market. The 2-piece wheel design does not offer as wide a range of application that a 3-piece wheel allows, however they are more common in the market and the prices start well below the average 3-piece wheel. Some 2-piece wheels have the center bolted into a cast or cast/spun rim section and other manufacturers press centers into spun rim sections and weld the unit together. When BBS developed a new 2-piece wheel to replace the previous 3-piece street wheel, they used the special rim-rolling technology (originally developed for racing wheels) to give the rim section the weight and strength advantages similar to a forged rim. On the high-end of the 2-piece wheel market you can find wheels using forged rims and forged centers. Since these are only sold in small volume and due to the high development and production costs associated with the forging process, they tend to be on the high end of the price scale.
Pro Tip: At Tire Rack, type in that you own a 1990 Mazda Miata. Then look at the 15" lightweight wheel selection.
Last edited by Shawn B
on 2015-04-04
at 16-34-07.