


Hmm. Well, I'll try my luck with 'DIY' garage' overhere. I'm sure they will have a press for wheel bearings and see what they can come up with.
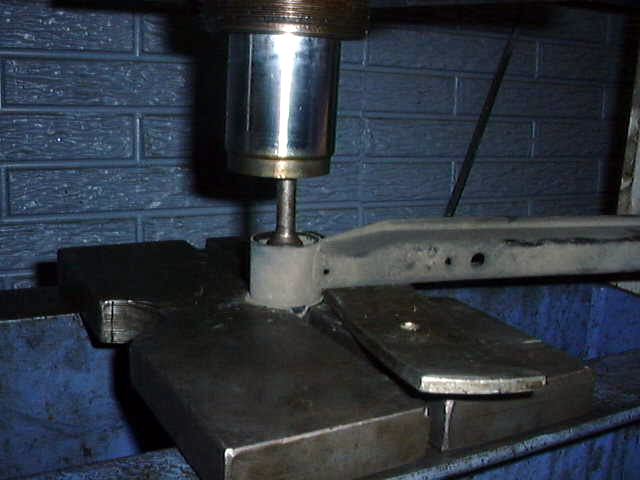
Now I'll look in to getting way more stronger then 4.8 rod bearing w/o ordering over internet for kicks, but all I would like to be able to do, is to do this on my own in my shed

its that sleeve thats making it a PITA thats why I burn mine out! I use a scroll saw with a nice blade to make it even more easier LOL! if it take more then 15 mins ill give my address and you can come punch me in my face! there its a win win!